Boost Manufacturing Quality Control with AI-Powered Defect Detection by DefectGuard
- pyadav52
- Jan 30
- 5 min read

Introduction
In the competitive world of manufacturing, product quality is paramount. Whether it’s ensuring consumer safety or meeting industry regulations, maintaining high standards is essential to a company’s reputation. Traditional quality control processes, however, often come with challenges—manual inspection is time-consuming, prone to errors, and can be costly. This is where DefectGuard, powered by cutting-edge AI defect detection technology, transforms quality control for manufacturers, offering the accuracy, efficiency, and scalability needed to meet today’s industry demands.
Why Quality Control Matters in Manufacturing
Product defects can be a significant financial burden, leading to costly returns, damaged brand reputation, and production delays. In today’s market, manufacturers face the pressure of delivering high-quality products consistently, at speed, and without error. Inconsistent inspection methods, especially manual ones, contribute to inefficiencies that hurt both the bottom line and product quality.
This is where AI-powered defect detection comes into play. By automating and enhancing the inspection process, AI solutions like DefectGuard ensure greater accuracy, faster throughput, and higher quality products. But what makes DefectGuard stand out among the growing AI solutions available for manufacturing?
Groundbreaking Features of DefectGuard: Efficiency and Accuracy at Its Core
1. Advanced Deep Learning Architecture
DefectGuard’s proprietary deep learning models are at the heart of its defect detection capabilities. These models are trained to detect defects with remarkable precision, achieving an impressive 99.8% accuracy rate across various manufacturing environments. The system continuously improves through machine learning, learning from new data with each inspection, ensuring that manufacturers benefit from ever-increasing accuracy.
2. Real-Time Multi-Point Inspection
Unlike traditional inspection methods, which focus on a single point at a time, DefectGuard allows for simultaneous multi-point inspection. This means multiple areas of a product can be checked at once, drastically improving throughput by 40% compared to manual or traditional automated systems.
3. Adaptive Lighting Technology
Manufacturers often deal with products of varying textures and materials that require different lighting conditions for proper inspection. DefectGuard incorporates adaptive lighting technology that automatically adjusts to varying surfaces and environmental conditions. This ensures consistent inspection quality, regardless of material or ambient light, eliminating the need for manual lighting adjustments and increasing efficiency.
4. Smart Defect Classification
DefectGuard goes beyond just detecting defects—it classifies them based on severity and type. This smart classification system offers manufacturers detailed insights into recurring problems, allowing for more informed decisions about process improvements and maintenance. It helps in proactive troubleshooting, reducing the risk of further defects and costly reworks.
5. Enhanced Edge Computing Integration
For truly real-time decision-making, DefectGuard integrates edge computing, allowing data to be processed on-site, near the production line. With latency reduced to under 50 milliseconds, manufacturers can instantly detect and address defects, preventing defective products from reaching the end of the production line.
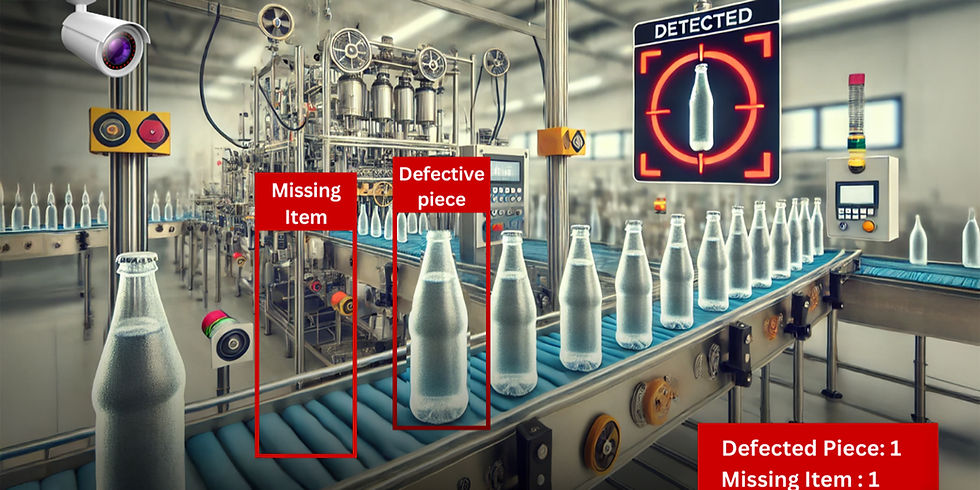
The Industry-Leading Benefits of DefectGuard
With these groundbreaking features, DefectGuard delivers powerful benefits that directly impact a manufacturer’s ROI and efficiency.
1. Cost Reduction
By automating defect detection and reducing the need for manual inspection, DefectGuard can lower labor costs by up to 75%. Additionally, early defect detection reduces waste by identifying flaws early in the production process, which helps prevent expensive rework or material waste.
2. Increased Efficiency
DefectGuard operates 24/7, unaffected by fatigue or human error, enabling continuous quality control without downtime. It can process hundreds of products per minute, offering a significant boost to throughput. This allows manufacturers to scale operations while maintaining consistently high-quality standards.
3. Quality Improvement
With AI-powered precision, DefectGuard is capable of detecting defects invisible to the human eye, ensuring higher-quality output. It maintains consistent inspection standards, providing the same level of accuracy and reliability during every inspection cycle. DefectGuard also generates detailed reports for compliance and performance optimization.
Revolutionary New Features for Proactive Quality Control
1. Predictive Maintenance Integration
One of the most exciting features of DefectGuard is its predictive maintenance integration. Powered by machine learning, the system can predict equipment failures before they impact production quality. This proactive approach reduces unplanned downtime by up to 30%, which is crucial for keeping production lines moving efficiently.
2. Advanced Material Recognition
DefectGuard automatically adapts its inspection settings to the material being processed, whether metal, plastic, textile, or any other material. This advanced material recognition ensures that inspections are always optimized, regardless of the type of material being worked on.
3. Cloud-Based Analytics Dashboard
Manufacturers can now view quality metrics in real-time with DefectGuard’s cloud-based analytics dashboard. This platform enables manufacturers to monitor performance across multiple production lines, access actionable insights, and make data-driven decisions to continuously improve production processes.
Challenges Addressed by DefectGuard
Here are some common manufacturing challenges that DefectGuard effectively addresses:
Manual Inspection Limitations: Traditional manual inspection is slow, inconsistent, and prone to human error. DefectGuard automates the entire defect detection process, reducing human intervention and improving accuracy.
Inspection Fatigue: Even automated systems can suffer from fatigue and inefficiency. DefectGuard operates continuously without lapses, ensuring reliable quality control around the clock.
Slow Detection and Response Time: Delays in defect detection can result in wasted time and material. DefectGuard uses real-time defect detection powered by edge computing, ensuring issues are caught instantly and addressed immediately.
Lack of Scalability: As production volumes grow, maintaining quality becomes harder. DefectGuard scales effortlessly to match increasing production demands, ensuring that quality standards are consistently met.
Use Cases of DefectGuard AI-Powered Defect Detection
1. Automotive Components
Use Case: Small cracks or defects in automotive parts like engine components can lead to severe failures. DefectGuard detects microfractures and flaws during production, ensuring components meet stringent safety standards before they are used in vehicles.
2. Electronics Assembly
Use Case: In electronics, even minor soldering defects or small component misplacements can cause malfunction. DefectGuard’s real-time, multi-point inspection identifies soldering defects and missing components, ensuring high-quality, fully functional devices.
3. Pharmaceutical Packaging
Use Case: Pharmaceutical products require precise packaging to ensure safety and compliance. DefectGuard identifies packaging defects like incorrect seals, damaged labels, or contamination, helping manufacturers comply with regulatory standards and preventing potential product recalls.
4. Food and Beverage Production
Use Case: In the food industry, packaging defects like poor seals or contamination can pose safety risks. DefectGuard inspects packaging materials for imperfections, ensuring that only safe, properly sealed products reach consumers and meet quality standards.
5. Textile Manufacturing
Use Case: Fabric defects such as weaving errors, color mismatches, and tears can be hard to detect manually. DefectGuard inspects textiles for defects, ensuring only flawless fabrics are sent to the market. It also helps detect dye inconsistencies or material wear, ensuring high-quality production for apparel and upholstery.
6. Furniture Manufacturing
Use Case: Furniture pieces are highly prone to defects such as cracks, misalignments, and surface imperfections. DefectGuard detects defects in wood, upholstery, and metal components, ensuring that only high-quality products reach consumers and reducing the risk of returns due to defective items.
7. Medical Device Assembly
Use Case: Medical devices require flawless precision during assembly to ensure patient safety. DefectGuard inspects every device for manufacturing defects, such as incorrect assembly or structural issues, ensuring they meet stringent medical standards before distribution.
The Future of Manufacturing Quality Control: DefectGuard Leads the Way
As the manufacturing landscape continues to evolve, DefectGuard is committed to driving innovation. By continuously improving our AI-driven technology, we ensure that our customers always have access to the most advanced defect detection solutions available. DefectGuard is not just about solving today’s quality control challenges—it’s about preparing manufacturers for the future of automated, AI-driven production.
Ready to Maximize ROI and Improve Quality Control?
If you’re looking to improve your quality control process, reduce costs, and enhance your manufacturing efficiency, DefectGuard is the solution you’ve been waiting for. Our AI-powered defect detection technology is designed to deliver measurable improvements across your operations, ensuring higher quality, reduced waste, and increased throughput.
Contact us today to schedule a demonstration of DefectGuard and see how our solutions can help you elevate your manufacturing quality control to the next level.
Comments